En la infraestructura crítica de casi todo proceso industrial, desde refinerías hasta plantas de alimentos, se encuentra un componente esencial: el intercambiador de calor. Su funcionamiento eficiente es fundamental para la rentabilidad y seguridad de cualquier operación. Sin embargo, para garantizar la fiabilidad de cada equipo, existe una fase crítica que a menudo se subestima en su complejidad: el diseño basado en estándares reconocidos. Aquí es donde las normas TEMA (Tubular Exchanger Manufacturers Association) se convierten en la brújula indispensable.
Un error en la selección del tipo TEMA no es un detalle menor; puede traducirse en sobrecostos significativos, fallas prematuras, tiempos de inactividad no planificados y, en última instancia, una merma en la eficiencia operativa que impacta directamente el balance final. En JAZAM, entendemos que la correcta aplicación de las Normas TEMA para Intercambiadores de Calor de Carcasa y Tubos es la piedra angular para garantizar un rendimiento óptimo y una larga vida útil del equipo. Nuestro compromiso es ir más allá del diseño estándar, utilizando simulación avanzada para ofrecer certeza predictiva.
En esta guía, desglosamos los principios, la clasificación y las consideraciones de diseño esenciales que todo profesional de la ingeniería y la gestión de planta debe conocer sobre los intercambiadores de calor de carcasa y tubos. Además, si busca una correcta especificación y un diseño térmico del intercambiador de calor hecho por expertos, le invitamos a conocer nuestros servicios.
¿Por qué las normas TEMA son indispensables? El impacto en sus resultados
La familiaridad con los detalles técnicos de TEMA puede parecer dominio exclusivo del ingeniero, pero sus implicaciones resuenan profundamente en los objetivos de cualquier gerente de planta o administrador.
- Reducción de riesgos operativos y mayor seguridad: Las normas TEMA establecen criterios rigurosos para la integridad estructural y funcional. Una selección y diseño TEMA adecuados minimizan el riesgo de fugas, fallas mecánicas y paradas inesperadas, protegiendo tanto la inversión como la seguridad del personal. Un equipo diseñado bajo estos estándares ofrece una póliza de seguro implícita contra sorpresas costosas.
- Control de costos de capital (CAPEX) y operativos (OPEX): Un diseño preciso, guiado por TEMA, evita el sobredimensionamiento innecesario del equipo, lo que se traduce en una optimización de la inversión inicial. A la vez, garantiza un rendimiento térmico esperado, evitando consumos energéticos excesivos para compensar ineficiencias, lo que impacta directamente en los costos operativos a lo largo de la vida útil del intercambiador.
- Fiabilidad y mantenimiento simplificado: La estandarización TEMA facilita el mantenimiento, la inspección y la disponibilidad de repuestos. Saber con precisión el tipo TEMA de un intercambiador agiliza cualquier intervención, minimizando el «downtime» y asegurando la continuidad de la producción.
En síntesis, aplicar correctamente Las normas TEMA para Intercambiadores de Calor de Carcasa y Tubos no es solo una buena práctica de ingeniería; es una decisión estratégica que se traduce en beneficios tangibles para el negocio.
Los fundamentos de TEMA: una clasificación crucial
Las normas TEMA proveen un sistema de clasificación de tres letras para definir la configuración de un intercambiador de calor de carcasa y tubos. Esta nomenclatura, universalmente reconocida, describe el cabezal frontal, el tipo de carcasa y el cabezal posterior. Comprenderla es el primer paso hacia una selección informada.
1. Nomenclatura e identificación TEMA (sistema de tres letras)
El código de tres letras de un intercambiador TEMA es esencial para su correcta identificación y diseño:
- Primera letra (cabezal frontal/de distribución): Define la configuración del cabezal delantero, por donde ingresa y sale el fluido del lado de los tubos. Ejemplos comunes incluyen «A» (cabezal con tapa removible) o «B» (cabezal integral).
- Segunda letra (tipo de carcasa): Indica la configuración de la carcasa. Los tipos más frecuentes son «E» (carcasa de un solo paso, la más común) o «K» (carcasa tipo kettle, usada en rehervidores).
- Tercera letra (cabezal posterior/de retorno): Especifica el diseño del cabezal trasero, por donde el fluido de los tubos realiza su retorno o sale del equipo. Tipos como «S» (espejo flotante) o «U» (tubos en U) son cruciales para manejar la expansión térmica.
Por ejemplo, un intercambiador AES denota un cabezal frontal tipo «A», una carcasa tipo «E» y un cabezal posterior tipo «S». Adicionalmente, el tamaño se especifica con dos números: el diámetro nominal de la carcasa en pulgadas y la longitud recta de los tubos.
2. Clases de servicio TEMA: más allá de la geometría
Las normas TEMA van más allá de la simple geometría, clasificando los intercambiadores según la severidad de su servicio, lo cual influye en los márgenes de diseño y las tolerancias de fabricación:
- Clase R (refinería): Destinada a las condiciones operativas más exigentes, típicas de las industrias de petróleo y gas. Estos equipos están diseñados para la máxima seguridad y confiabilidad, con tolerancias más estrictas y características para manejar fluidos sucios, de alta viscosidad o corrosivos.
- Clase C (comercial): Aplicable a condiciones moderadas, adecuadas para procesos comerciales y generales donde los requisitos de seguridad y rendimiento son importantes, pero menos extremos que en refinerías.
- Clase B (básico): Diseñada para la industria química de procesos, ofreciendo una solución más económica para servicios menos rigurosos.
Es vital no solo indicar el tipo TEMA (ej. AES), sino también la clase (R, C o B) en la fase de diseño, ya que esto impacta directamente en las especificaciones mecánicas y los costos asociados.
Consideraciones clave en el diseño térmico y mecánico según TEMA
La elección del tipo TEMA y su correcta aplicación influyen en aspectos críticos del diseño que determinan el rendimiento y la durabilidad del intercambiador.
Arreglo y número de tubos:
- Dimensiones: Los diámetros de los tubos varían comúnmente entre 5/8 y 1 1/4 de pulgada. El espesor se define por el calibre BWG (Birmingham Wire Gauge), que típicamente va del 10 al 20.
- Patrones de tubos: Los arreglos de tubos más comunes son cuadrado, cuadrado girado 45° y triangular. Para hidrocarburos o fluidos viscosos, se recomienda el arreglo cuadrado o cuadrado girado 45°.
- Pasos por los tubos: Los «pasos» se refieren a la cantidad de veces que el fluido del lado de los tubos cambia de dirección dentro del haz tubular. Un mayor número de pasos aumenta la velocidad del fluido y, por ende, la transferencia de calor, pero también incrementa la caída de presión. El número máximo de pasos recomendados por los tubos es de 4 para diámetros de tubo menores a 250 mm (10 pulgadas). 5Si el diámetro está entre 50 mm y 510 mm (aproximadamente 2 a 20 pulgadas), el número de pasos puede aumentar.
- Tubos en «U»: La configuración de tubos en «U» es particularmente útil para manejar la dilatación térmica diferencial. Esto ocurre cuando la carcasa y los tubos se expanden o contraen a diferentes ritmos debido a las distintas temperaturas de los fluidos. Los tubos en «U» permiten esta expansión sin generar estrés mecánico, prolongando la vida útil del equipo y evitando fallas estructurales.
Placas deflectoras (baffles):
- Función: Las placas deflectoras, como las segmentadas simples, son esenciales para dirigir el flujo del fluido en la carcasa, promoviendo la turbulencia y, por ende, mejorando significativamente el coeficiente de transferencia de calor.
- Diseño especial: En intercambiadores con espejos fijos y múltiples pasos por la carcasa, se emplea una mampara longitudinal continua, soldada a la envolvente, para separar los flujos.
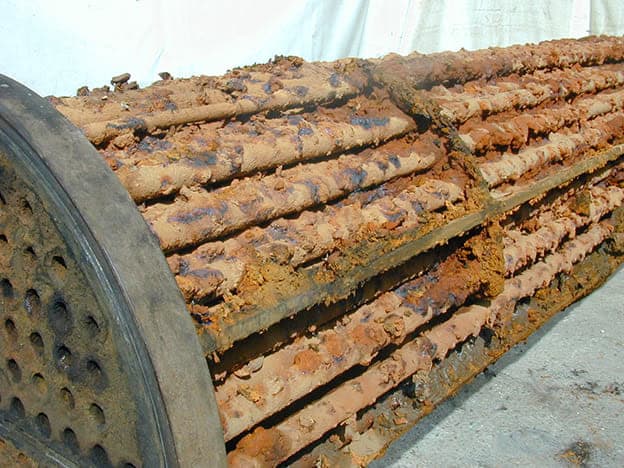
Protección del haz de tubos (placa de choque o impingement plate):
- Necesidad: Para prevenir el desgaste excesivo por impacto o erosión del fluido a alta velocidad en las boquillas de entrada/salida, el haz de tubos debe protegerse. Esto se logra con una placa de choque, un cinturón de distribución, o una ampliación de la boquilla.
- Restricciones: Es importante destacar que TEMA no permite el uso de placas de choque perforadas o ranuradas. Su requerimiento se basa en la sección RCB-4.6 de TEMA 9ª Edición.
Diseño de boquillas:
- Caída de presión crítica (ΔP): La caída de presión en las boquillas es un factor determinante. Para fluidos monofásicos, no debe exceder el 5% de la pérdida de presión total del equipo. Para fluidos bifásicos (líquido/vapor), el límite es del 12%. Esto es vital para controlar vibraciones y optimizar el flujo.
Espejos (tubesheets) y cabezales:
- Integridad estructural: El diseño de los espejos debe cumplir estrictamente con la sección UHX de ASME Sección VIII, División 1:2010, y su espesor no debe ser inferior al requerido por TEMA 9ª edición, clase R.
- Sellado: Las ranuras de sellado en los barrenos de los espejos para la inserción de los tubos deben cumplir con el párrafo RB-7.24 del estándar TEMA. 13
Materiales de construcción y consideraciones de corrosión:
- Compatibilidad: La selección de materiales es crítica y se basa en la compatibilidad con los fluidos de proceso, las condiciones de operación (temperatura y presión de diseño, tolerancia a la corrosión) y los requisitos mecánicos.
- Margen de corrosión: La corrosión permisible debe especificarse por separado para el lado de la carcasa y el lado de los tubos y se añade a los espesores mínimos calculados. Sin embargo, para tubos de transferencia, mamparas y placas de soporte, no se añade espesor por corrosión a menos que la hoja de datos lo exija.
Presión y temperatura de diseño:
- Criterios de diseño: La carcasa del intercambiador, al ser un recipiente a presión, se diseña siguiendo códigos como ASME Sección VIII, División 1. 17La presión interna de diseño debe ser el valor más alto esperado en condiciones normales a la temperatura de diseño.
Presión y temperatura de diseño:
- Tolerancias: Las normas TEMA establecen pautas precisas para la fabricación, incluyendo tolerancias dimensionales.
- Pruebas no destructivas: La inspección radiográfica es obligatoria para las soldaduras a tope en la carcasa, canal y canal de retorno (según NRF-028-PEMEX-2010). 20Las placas con espesores superiores a 50.8 mm (2 pulgadas) deben inspeccionarse por ultrasonido (según ASME SA-435).
Para asegurar una convergencia óptima y un diseño que equilibre rendimiento y costo, consulte nuestros servicios de ingeniería especializada.
La ventaja JAZAM: de la simulación a la certeza predictiva
La aplicación manual de los estándares TEMA es fundamental para la comprensión de los principios, pero en la ingeniería moderna, la complejidad de los procesos exige una precisión que solo la simulación avanzada puede ofrecer. En JAZAM, vamos más allá de las correlaciones empíricas. Utilizamos herramientas de simulación de vanguardia como ASPEN EDR para validar cada aspecto del rendimiento antes de la fabricación.
Esto nos permite:
- Optimizar la geometría: Determinar el equilibrio perfecto entre la máxima transferencia de calor y la mínima caída de presión. Con ASPEN EDR, podemos iterar rápidamente entre diferentes configuraciones de tubos, baffles y diámetros de carcasa para encontrar la solución más eficiente y rentable.
- Predecir el comportamiento: Simular con precisión cómo operará el equipo bajo diversas condiciones, identificando riesgos potenciales antes de que se conviertan en costosos problemas. Esto incluye prever el impacto de los factores de ensuciamiento y las variaciones en las propiedades de los fluidos.
- Garantizar el rendimiento: Entregar un diseño que cumple con las especificaciones desde el primer día, validado por un modelo predictivo riguroso. Esto reduce la incertidumbre del proyecto y ofrece una seguridad sin igual para su inversión.
Nuestro enfoque no solo se basa en los fundamentos de TEMA, sino que los potencia con la capacidad de cómputo para explorar un vasto universo de posibilidades de diseño, asegurando la solución más eficiente y robusta para su aplicación específica.