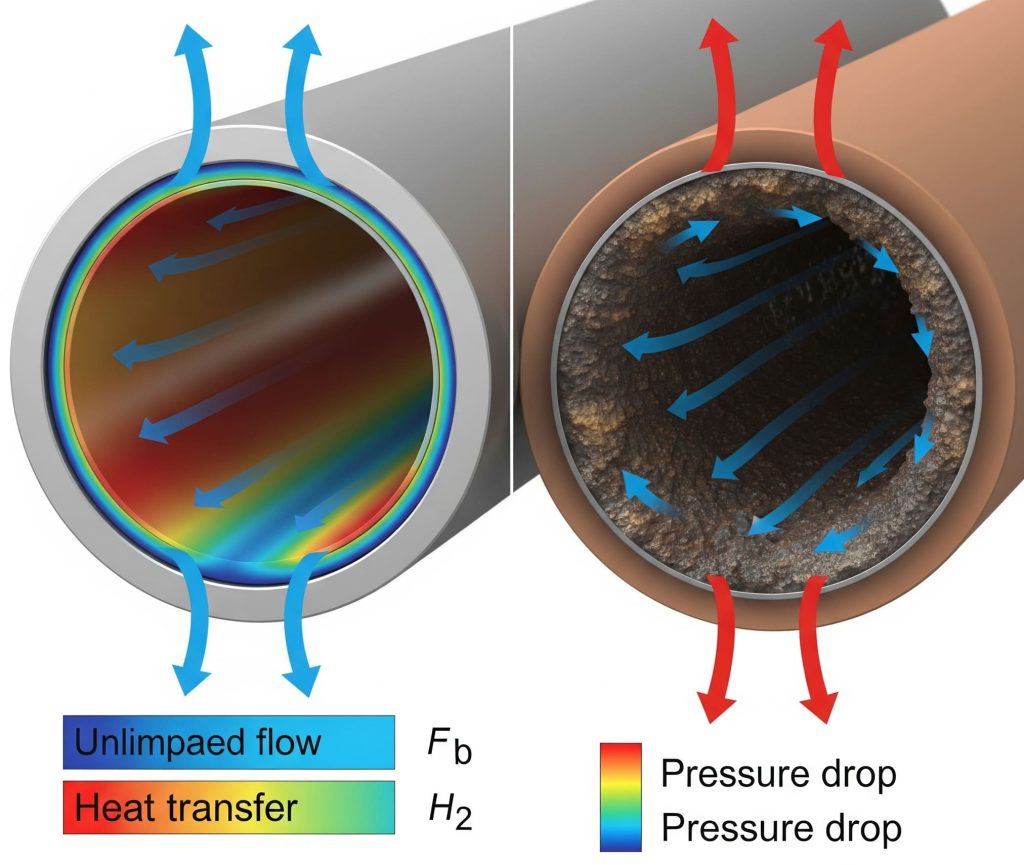
En el corazón de todo proceso industrial opera un enemigo silencioso y costoso: el fouling en intercambiadores de calor. Este fenómeno, la acumulación progresiva de depósitos no deseados en las superficies de transferencia de calor, es la causa raíz de innumerables sobrecostos operativos y paradas de planta no programadas. Es una arteria crítica que se obstruye lentamente, ahogando el rendimiento, la eficiencia y la rentabilidad de su operación.
Para un gerente, el fouling se traduce directamente en facturas energéticas más altas, ciclos de mantenimiento imprevistos y una reducción de la capacidad productiva, impactando de lleno en el OPEX. Para un ingeniero, significa una batalla constante contra una caída de presión creciente y un rendimiento térmico deficiente. En JAZAM, comprendemos que la solución más rentable no es la reacción tardía con limpiezas costosas, sino la anticipación estratégica. La clave reside en un diseño experto que anticipe el problema desde el origen. Esta guía definitiva le proporcionará las herramientas para diagnosticar, combatir y, lo más importante, diseñar sistemas robustos al ensuciamiento.
Diagnóstico del problema: 4 indicadores clave de que el fouling está actuando
Detectar el ensuciamiento a tiempo es fundamental para controlar sus costos. Para cuantificar su impacto, debe monitorear estos cuatro indicadores clave en sus equipos:
1. Aumento de la caída de presión (ΔP)
Este es el primer y más evidente síntoma. Si la caída de presión en su equipo aumenta por encima de los valores de diseño sin que el caudal haya variado, es una prueba irrefutable de una obstrucción física. Las partículas o depósitos reducen el área de flujo, forzando a las bombas a trabajar más para mantener el proceso. Esto no es solo un indicador técnico; es un gasto directo y medible en su factura eléctrica y un riesgo para la integridad de su sistema de bombeo.
2. Reducción del coeficiente global de transferencia de calor (Uo)
Esta es la señal definitiva de una pérdida de rendimiento térmico. Los factores de ensuciamiento típicos (Rf) pueden parecer pequeños, del orden de 10⁻⁴ m²·°C/W, pero su efecto es devastador: son equivalentes a añadir una capa de caliza de 0.2 mm de espesor, un aislante muy eficaz. Una disminución del valor de Uo indica que una de estas capas está impidiendo el paso del calor.
El procedimiento correcto para verificarlo se realiza utilizando software de simulación especializado como Aspen EDR. Al introducir los parámetros operativos actuales (caudales, temperaturas) y la geometría exacta del equipo en un módulo de evaluación (rating), el software calcula el grado de ensuciamiento real. Este análisis revela con precisión cuánto ha disminuido el coeficiente Uo en comparación con su estado limpio de diseño. Comprender cómo aplica el manual completo sobre el fouling en intercambiadores: diagnóstico, prevención y diseño robusto es crucial para la longevidad del equipo.
3. Variación en las temperaturas de salida del proceso
Este es un síntoma directo de que el intercambiador ya no cumple con su deber térmico (Q). La capa de fouling actúa como un aislante, impidiendo que el equipo realice el trabajo para el que fue diseñado. Esto se manifiesta de dos maneras: el fluido caliente no logra enfriarse a su temperatura de diseño (sale más caliente de lo esperado), o viceversa, el fluido frío no alcanza la temperatura objetivo (sale más frío de lo que debería). Cualquiera de estos escenarios puede causar problemas de calidad, bajo rendimiento en etapas posteriores del proceso y un derroche general de energía.
4. Ciclos de limpieza y mantenimiento acelerados
Desde una perspectiva de negocio, este es uno de los indicadores más dolorosos. Los factores de ensuciamiento tabulados, como los de Kern, buscan asegurar un período de operación de 1 a 1.5 años entre limpiezas. Sin embargo, este tiempo es una referencia y puede variar drásticamente dependiendo de la severidad de los fluidos en cuestión. Si su equipo requiere paradas para mantenimiento con una frecuencia mucho mayor a la planificada para su servicio específico, es una señal inequívoca de que el fouling es más severo de lo estimado en el diseño, afectando directamente la rentabilidad.
Anatomía del enemigo: los mecanismos del fouling
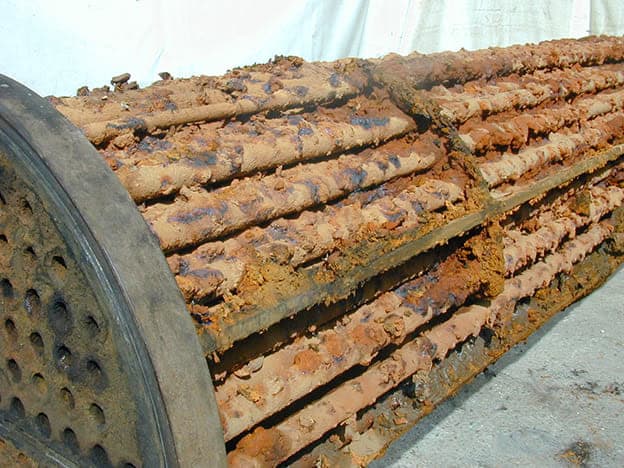
Para combatir el ensuciamiento, primero hay que entender su naturaleza. Se manifiesta a través de seis mecanismos principales que a menudo actúan en conjunto:
- Cristalización: Formación de depósitos sólidos como el carbonato de calcio, especialmente cuando la solubilidad de las sales disminuye al aumentar la temperatura.
- Asentamiento (sedimentación): Acumulación de partículas suspendidas como lodos, óxidos o arenas sobre la superficie.
- Reacción química: Productos de reacciones en la superficie, como la degradación térmica de crudos a altas temperaturas de pared.
- Corrosión: Formación de óxidos o subproductos de la corrosión del propio metal que se adhieren a la superficie.
- Biológico: Crecimiento de microorganismos como algas y hongos, común en sistemas con agua de enfriamiento.
Congelación/solidificación: Solidificación de un componente del fluido sobre una superficie fría.
El plan de batalla: un diseño robusto como primera línea de defensa
La lucha contra el fouling se gana en la mesa de diseño. Un enfoque de ingeniería robusto puede minimizar drásticamente la tasa de ensuciamiento. Un correcto entendimiento de este manual completo sobre el fouling en intercambiadores: diagnóstico, prevención y diseño robusto es el primer paso.
1. Ubicación estratégica de los fluidos
- Fluido sucio por los tubos: Siempre que sea posible, el fluido con mayor potencial de ensuciamiento debe circular por el interior de los tubos para facilitar la limpieza mecánica.
- Fluido viscoso por la carcasa: Para minimizar la caída de presión, los fluidos muy viscosos se benefician del área de flujo transversal mayor que ofrece el lado de la carcasa.
- Fluido a alta presión por los tubos: Por seguridad y costo, es preferible contener altas presiones dentro de los tubos.
2. Control riguroso de las velocidades
La velocidad es crítica. Debe ser alta para «barrer» depósitos, pero sin causar daños.
- Rangos de referencia: Para líquidos, entre 0.7 y 7 m/s; para gases, de 3 a 30 m/s. Para agua de enfriamiento, se recomiendan 2 m/s en tubos para mitigar el fouling.
- Límites y responsabilidad: TEMA no limita las velocidades erosivas, pero como ingenieros, es nuestro deber evitarlas para prevenir vibraciones (acústicas, hidraelásticas) y desgaste. Una buena práctica es limitar la caída de presión en las boquillas a no más del 5% del ΔP total para líquidos y 12% para vapor, controlando así las vibraciones en la entrada.
3. Selección inteligente de materiales y geometría
- Materiales: La elección correcta de la metalurgia es fundamental. Se usan aceros al carbono como SA 516 para altos esfuerzos, pero para servicios corrosivos o con H₂S, se debe recurrir a aceros aleados o inoxidables y cumplir con normas estrictas como ISO 15156 o NACE-MR0103, incluyendo mediciones de dureza.
- Geometría: Para fluidos muy sucios, se recomiendan tubos de 1 pulgada de diámetro. Los bafles suelen tener cortes del 20-40% para guiar el flujo. Es crucial saber que si el diámetro del tubo es menor a 50 mm (2″), el número máximo de pasos es 4. Las placas de impacto (impingement plates) en las boquillas son esenciales y obligatorias por TEMA para proteger los tubos de la erosión.
4. Prácticas de operación y mantenimiento eficientes
Un buen diseño debe complementarse con una operación inteligente.
- Pre-tratamiento: Instalar filtros o separadores antes del intercambiador es una inversión que protege todo el sistema.
- Limpieza programada: Utilice métodos adecuados al tipo de ensuciamiento. La limpieza química con aceite lavador o la mecánica con escobillas son comunes. La inmersión de haces en tinas con diésel es otra técnica documentada.
- Precaución de seguridad crítica: Nunca limpie tubos de forma individual con vapor. La expansión térmica diferencial puede generar esfuerzos enormes y dañar permanentemente el equipo.
La ventaja JAZAM: de la simulación a la certeza predictiva
Herramientas como Aspen EDR son potentes, pero su valor depende de la pericia del ingeniero. A continuación, se explican los modos de uso para entender su poder.
El poder de la simulación: Rating, Diseño y Simulación
- Evaluación (Rating): Este modo se usa para verificar el desempeño de un intercambiador existente. Se ingresan las dimensiones exactas del equipo y las condiciones de operación actuales. El software calcula el rendimiento real, cuantifica el efecto del fouling y nos dice si el equipo cumple su deber térmico. Es ideal para diagnosticar problemas y programar limpiezas de manera informada.
- Diseño (Design): Se utiliza para crear un intercambiador nuevo desde cero. Se ingresan los parámetros del proceso (calor a transferir, propiedades de fluidos, temperaturas) y el software propone la geometría óptima (dimensiones, número de tubos, tipo de coraza) para cumplir los requerimientos de la forma más eficiente.
- Simulación (Simulation): Se emplea para predecir cómo se comportará un diseño existente bajo diferentes condiciones. Partiendo de una geometría conocida, se pueden variar los flujos o temperaturas de entrada para realizar estudios «qué pasaría si…». Esto es invaluable para optimizar la operación y validar el comportamiento del equipo ante cambios en el proceso.
En JAZAM, no solo usamos estas herramientas; las integramos en un proceso riguroso. Validamos los resultados con datos de planta y, si es necesario, con un segundo simulador. No entregamos un cálculo, sino certeza predictiva, mitigando su riesgo de inversión (CAPEX) y de operación (OPEX).