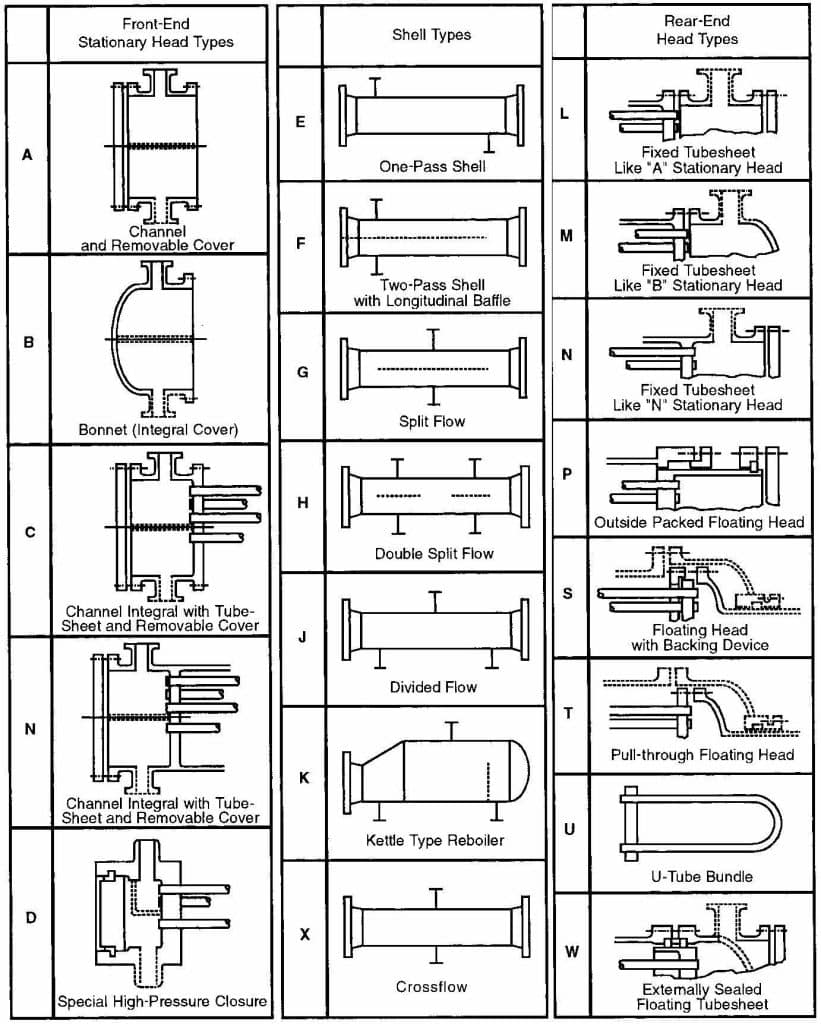
In the critical infrastructure of nearly every industrial process, from refineries to food plants, lies an essential component: the heat exchanger. Its efficient operation is fundamental to the profitability and safety of any operation. However, to ensure the reliability of each unit, there is a critical phase whose complexity is often underestimated: design based on recognized standards. This is where the TEMA (Tubular Exchanger Manufacturers Association) standards become the indispensable compass.
An error in selecting the TEMA type is not a minor detail; it can translate into significant cost overruns, premature failures, unplanned downtime, and ultimately, a decrease in operational efficiency that directly impacts the bottom line. At JAZAM, we understand that the correct application of the TEMA standards for shell and tube heat exchangers is the cornerstone for ensuring optimal performance and a long service life for the equipment. Our commitment is to go beyond standard design, using advanced simulation to offer predictive certainty.
In this guide, we break down the essential principles, classification, and design considerations that every engineering and plant management professional should know about shell and tube heat exchangers. Furthermore, if you are looking for a correct specification and an expert-led thermal design of a heat exchanger, we invite you to learn about our services.
Why are TEMA standards indispensable? The impact on your results
Familiarity with the technical details of TEMA may seem like the exclusive domain of the engineer, but its implications resonate deeply with the objectives of any plant or administrative manager.
Reduced operational risks and increased safety: TEMA standards establish rigorous criteria for structural and functional integrity. A proper TEMA selection and design minimize the risk of leaks, mechanical failures, and unexpected shutdowns, protecting both the investment and personnel safety.
Control of capital (CAPEX) and operating (OPEX) costs: A precise design, guided by TEMA, avoids unnecessary oversizing of the equipment, which translates into an optimization of the initial investment. At the same time, it guarantees expected thermal performance, preventing excessive energy consumption.
Reliability and simplified maintenance: TEMA standardization facilitates maintenance, inspection, and the availability of spare parts. Knowing the precise TEMA type of an exchanger streamlines any intervention, minimizing downtime and ensuring production continuity.
In summary, correctly applying the TEMA standards for shell and tube heat exchangers is not just good engineering practice; it is a strategic decision that translates into tangible benefits for the business.
The fundamentals of TEMA: a crucial classification
TEMA standards provide a three-letter classification system to define the configuration of a shell and tube heat exchanger. This universally recognized nomenclature describes the front head, the shell type, and the rear head. Understanding it is the first step toward an informed selection.
1. TEMA nomenclature and identification (three-letter system)
The three-letter code of a TEMA exchanger is essential for its correct identification and design:
First letter (front/channel head): Defines the configuration of the front head. Common examples include “A” (channel with removable cover) or “B” (bonnet-type head).
Second letter (shell type): Indicates the shell configuration. The most frequent types are “E” (single-pass shell) or “K” (kettle-type shell, used in reboilers).
Third letter (rear/return head): Specifies the design of the rear head. Types like “S” (floating tubesheet) or “U” (U-tube) are crucial for handling thermal expansion.
For example, an AES exchanger denotes an “A” type front head, an “E” type shell, and an “S” type rear head.
2. TEMA service classes: beyond geometry
TEMA standards go beyond simple geometry, classifying exchangers according to the severity of their service:
Class R (refinery): Intended for the most demanding operating conditions, typical of the oil and gas industries, designed for maximum safety and reliability.
Class C (commercial): Applicable to moderate conditions for commercial and general processes.
- Class B (basic): Designed for the chemical process industry, offering a more economical solution for less rigorous services.
It is vital not only to indicate the TEMA type but also the class (R, C, or B) in the design phase, as this directly impacts the mechanical specifications and costs.
Key considerations in thermal and mechanical design according to TEMA
The choice of TEMA type and its correct application influence critical design aspects that determine the exchanger’s performance and durability.
Tube arrangement and number:
Dimensions: Tube diameters commonly vary between 5/8 and 1 1/4 inches, with thickness defined by BWG.
Tube patterns: Common layouts are square, rotated square (45°), and triangular. For viscous fluids, the square or rotated square layout is recommended.
Tube passes: A higher number of passes increases fluid velocity and heat transfer but also increases pressure drop. The maximum recommended number of passes is 4 for tube diameters less than 250 mm (10 inches).
U-tubes: The U-tube configuration is useful for handling differential thermal expansion without generating mechanical stress.
Baffles:
Function: Baffles are essential for directing fluid flow in the shell, promoting turbulence and improving the heat transfer coefficient.
Special design: In exchangers with fixed tubesheets and multiple shell passes, a continuous longitudinal baffle is used to separate the flows.
Tube bundle protection (impingement plate):
Necessity: To prevent erosion by high-velocity fluid at the nozzles, an impingement plate, distribution belt, or expanded nozzle is required.
Restrictions: TEMA does not permit the use of perforated or slotted impingement plates, based on section RCB-4.6 of TEMA 9th Edition.
Nozzle design:
- Critical pressure drop (ΔP): For single-phase fluids, the pressure drop in the nozzles should not exceed 5% of the total equipment pressure loss. For two-phase fluids, the limit is 12%.
Tubesheets and heads:
Structural integrity: The design must comply with ASME Section VIII, Division 1, and their thickness must not be less than that required by TEMA 9th edition, class R.
Sealing: The sealing grooves for tube insertion must comply with paragraph RB-7.24 of the TEMA standard.
Materials of construction and corrosion considerations:
Compatibility: Material selection is based on compatibility with process fluids and operating conditions.
Corrosion allowance: This must be specified for the shell and tube sides and is added to the minimum calculated thicknesses. No corrosion allowance is added for transfer tubes, baffles, and support plates unless specified.
Design pressure and temperature:
- Design criteria: The exchanger shell is designed following codes like ASME Section VIII, Division 1. The internal design pressure is the highest value expected under normal conditions.
Tolerances and testing:
- Tolerances: TEMA standards establish precise guidelines for manufacturing and dimensional tolerances.
Nondestructive testing: Radiographic inspection is mandatory for certain butt welds. Plates thicker than 50.8 mm (2 inches) must be inspected by ultrasound.
To ensure optimal convergence and a design that balances performance and cost, consult our specialized engineering services.
The JAZAM advantage: from simulation to predictive certainty
The manual application of TEMA standards is fundamental, but modern engineering demands a precision that only advanced simulation can offer. At JAZAM, we use tools like ASPEN EDR to validate every aspect of performance before manufacturing.
This allows us to:
Optimize geometry: Determine the perfect balance between maximum heat transfer and minimum pressure drop.
Predict behavior: Accurately simulate how the equipment will operate under various conditions, identifying risks before they become problems.
Guarantee performance: Deliver a design that meets specifications from day one, validated by a rigorous predictive model.
Our approach enhances TEMA fundamentals with computational power, ensuring the most efficient and robust solution for your specific application.
Conclusion: A strategic framework for success
Ultimately, the TEMA standard is more than a technical document; it is a strategic framework that aligns engineering precision with business objectives. It provides a common language that ensures reliability, controls costs, and maximizes safety. A design that correctly interprets and applies these principles is not an expense, but a fundamental investment in the long-term operational health and profitability of your plant.